Обзор методик техобслуживания и ремонта оборудования системы управления производственными активами предприятия
- Подробности
- Опубликовано: 07.09.2021 11:27
- Автор: Абазьева Мария Павловна
- Просмотров: 5140
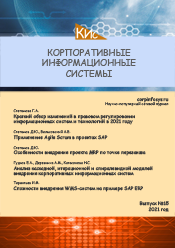
Аннотация: в статье рассмотрены существующие методики технического обслуживания и ремонта оборудования: ГОСТ Р 27.606–2013, ГОСТ Р 55234.3–2013, стандарт SAE JA1011 Evaluation Criteria for Reliability Centered Maintenance Processes, которые используются на предприятиях в системе управления его производственными активам. Дан их обзор, описана последовательность и приведены примеры шагов каждой рассмотренной методики ТОиР.
Скачать: PDF (статья), PDF (выпуск №15).
Ключевые слова: методы технического обслуживания и ремонта, управление ремонтами и техническим обслуживанием, техническое обслуживание и ремонт, управление техническим обслуживанием и ремонтами, ремонт и обслуживание оборудования, подходы к техническому обслуживанию, система технического обслуживания и ремонта, техническое обслуживание между ремонтами, техническое обслуживание предприятий, методы организации ремонта и технического обслуживания.
Введение
Для успешного запуска системы управления производственными активами необходимо изучить и внедрить методики технического обслуживания и ремонта оборудования (далее ТОиР). Для этого в компании формируются целые отделы и департаменты, что в дальнейшем оправдывает такой подход. Запуск информационной системы управления производственными активами, не зависимо от того какую выбрала компания (SAP Plant Maintenance, TRIM и тд), без использования методик ТОиР не принесет эффективности, которую ожидают получить от нее бизнес-пользователи.
В одной статье довольно сложно раскрыть все существующие методики для формирования стратегического подхода к управлению производственными активами. Поэтому были выбраны три методики, внедрение которых можно встретить на предприятиях: обслуживание, ориентированное на безотказность (Reliability Centered Maintenance, RCM), анализ первопричин (Root Cause Analysis, RCA) и мониторинг активов с учетом фактора риска (Risk-Based Inspection, RBI).
1. Обслуживание, ориентированное на безотказность
В ГОСТ Р 27.606–2013 можно найти определение RCM как «надежностно-ориентированное техническое обслуживание» [2]. Данная методика берет свое начало в авиапромышленности. В 1968 было разработано представителями нескольких авиакомпаний руководство MSG-1 «Maintenance Evaluation and Program Development» («Оценка ТО и разработка программы»). Последующее развитие и усовершенствование методики позволило применять ее и в других отраслях промышленности. В 1999 году был выпущен стандарт SAE JA1011 Evaluation Criteria for Reliability Centered Maintenance Processes (RCM).
Основная цель RCM – обеспечение надежности критичных для деятельности предприятия производственных и технологических процессов. Акцент смещен именно на поддержание надежности процессов предприятия, а не поддержания в надлежащем состоянии производственных активов: выполняются только необходимые ремонтные воздействия, что позволяет снизить стоимость работ на техническое обслуживание активов. Методика строится на так называемом RCM-анализе. Суть анализа состоит в подборе набора необходимых мер, которые будут гарантировать выполнение производственных функций, которые ожидаются от производственных активов.
Первое, что должно быть выполнено – это определение ресурса или системы, для которого будет использовать принципы RCM. Это могут быть как все активы предприятия, так и часть их них. Владельцам активов необходимо тщательно подойти к выбору активов, так как применение принципов RCM требует времени и высокой компетенции персонала.
Далее определяются функции актива. Функции могут быть первичными (например, автомобиль, который может перевозить до 5 пассажиров) и вторичными (автомобиль, с экологическим классом ЕВРО-5). После задаются функциональные отказы и их причины. Определяется отказ конкретной функции, а не отказ актива в целом. Например, автомобиль перевозит 4 пассажиров вместо заявленных 5. Причина отказа – повреждение ремня безопасности 5-го пассажира.
Кроме того необходимо определить последствия отказов. На данном этапе должно быть выполнено описание последствий отказов. Например, при повреждении ремня безопасности пассажир автомобиля может получить травмы при ДТП. И в заключении задаются воздействия для предотвращения отказа, определяется периодичность проведения воздействий (проверка механизма защелкивания ремня при каждом ТО). Также здесь вводятся признаки, по которым можно определить скорое наступление отказа (как пример, заедает механизм защёлкивания ремня). На основе выполненного RCM-анализа, формируется перечень операций для оптимальной стратегии ТОиР.
2. Анализ первопричин
RCA – это пошаговая методика, которая используется для выявления основной причины неисправности. Метод применятся во многих сферах: управление производственными процессами, информационные технологии, медицине, производстве и промышленности. Основная цель RCA в ТОиР – определить причину отказа. Причины отказов оборудования по методике RCA делятся на четыре типа:
- человеческий фактор (персонал сделал что-то не так или не сделал вовсе);
- организационная причина (неоптимально выстроенные рабочие процессы персонала);
- материальные причины (повреждение оборудования и/или его узлов, которое не позволяет полноценно функционировать);
- операционные причины (ошибочные расчеты, что привело к перегрузке оборудования и вывода его из строя).
Первое, что выполняется в анализе RCA – определение проблемы. Описываются сама проблема и симптомы отказов. Далее ведется сбор данных. Выполняется расследование для установления фактов происшествия, и определяются последствия отказа. На этом и дальнейших этапах активно участвуют эксперты, которые глубоко знакомы с проблемой и могут помочь с пониманием корневой причины отказа. Для качественного сбора данных может потребоваться достаточно продолжительное время, которым не всегда располагает персонал предприятия. Это является одной из причин сложности использования методики RCA.
Далее определяются все возможные причины отказов, и ведется поиск коренной причины [1]. На данном шаге для анализа можно использовать следующие методы: «5 почему», причинно-следственная связь, анализ дерева отказов и ситуационный анализ. После чего разрабатываются решения по устранению неисправностей. Здесь выполняется поиск эффективного решения по устранению отказов и его внедрение (табл. 1).
Табл. 1. Пример определения причин отказа и возможных решений
Проблема | Причина | Возможные решения |
Высокая температура масла в гидросистеме машины | Уровень масла, ниже минимально установленного по нормативу | Привести уровень масла к установленному значению |
Не отрегулированы предохранительные и редукционные клапана | Отрегулировать клапана |
В заключении ведется оценка эффективности внедренных решений по устранению отказов. Здесь должны быть разработаны показатели эффективности. RCA является удобным инструментом для понимания коренных причин отказов оборудования. Информация, полученная в ходе данного анализа, помогает предотвратить такие отказы в будущем.
3. Мониторинг активов с учетом фактора риска
Методика RBI позволяет определить оптимальные объемы и периодичность мониторинга активов на основе анализа рисков отказа. Данная методика была разработана американским институтом нефти для предприятий нефтяной и нефтехимической промышленности. Нормативными документами, описывающими организацию процесса RBI, являются:
- API-580 Risk-based Inspection;
- API-581 Risk-Based Inspection Technology;
- CWA 15740:2008 Risk-Based Inspection and Maintenance Procedures for European Industry (RIMAP);
- ГОСТ Р 55234.3–2013 Процедуры проверки и технического обслуживания на основе риска является адаптированной версией CWA 15740:2008.
Анализ RBI выполняется в следующем порядке: сбор данных. Необходимо собрать данные по оборудованию и связанной с ней нормативной документацией. Собранные данные будут использоваться для оценки вероятности и последствия отказов. Например, история осмотров и ремонтов, регламенты по эксплуатации и т. д.
Далее осуществляется идентификация отказов. Здесь определяются возможные сценарии отказа (например, от трещины до разрыва) на основе ожидаемых механизмов повреждения. После проводится оценка последствий отказа в следующих категориях:
- влияние на общественную безопасность;
- безопасность сотрудников;
- окружающую среду и прямые/косвенные финансовые затраты.
Кроме того оценивается вероятности того, что произойдет отказ: вероятность того, что часть оборудования выйдет из строя в определенный момент времени. Данный этап является самым сложным, так как требует понимания механизмов отказа и умение распознавать будущие изменения. Каждый сценарий отказа должен быть оценен, чтобы определить вероятность его возникновения.
После этого осуществляется ранжирование рисков и установка интервалов инспекции. Зная вероятность и последствия наступления рисков, используя матрицу ранжирования рисков, определяется поле, в котором находится данный риск. Матрица позволяет установить уровень риска для каждой единицы оборудования и установить интервалы инспекций. Это позволяет направить максимальные усилия на оборудование в критичной зоне рисков. Матрица рисков разрабатывается отдельно в каждой компании (табл. 2).
Табл. 2. Пример матрицы рисков
Проблема | Вероятность | ||||
Крайне вероятно |
Маловероятно | Возможно | Вероятно | Очень вероятно |
|
Очень высокий уровень | Ниже среднего | Средний | Выше среднего | Высокий | Высокий |
Высокий уровень | Низкий | Ниже среднего | Средний | Выше среднего | Высокий |
Средний уровень | Низкий | Ниже среднего | Средний | Средний | Выше среднего |
Низкий уровень | Низкий | Ниже среднего | Ниже среднего | Средний | Средний |
Очень низкий уровень | Низкий | Низкий | Ниже среднего | Средний | Средний |
Категория: безопасность персонала | Отсутствуют травмы либо они незначительны | Травмы с лёгкой степенью тяжести | Травмы со средней степенью тяжести | Травмы с высокой степенью тяжести | Травмы со смертельным исходом |
Позже ведется подготовка плана по снижению риска. План должен соответствовать уровню риска и учитывать ожидаемый отказ, режимы и ключевые факторы, влияющие на риск. План может включать в себя такие действия как: осмотр оборудования изнутри, а не только внешний осмотр, модернизацию оборудования и его узлов, изменение регламента обслуживания и т. д.
Оценка рисков должна регулярно обновляться, что дает возможность определить эффективность выбранных методов по их снижению. Переоценку необходимо выполнять, например, после получения новых данных проверки, внесения изменений в конструкцию оборудования. В процессе RBI-анализа выполняется описание компонентов оборудования, анализ технологических данных, проводится оценка вероятности и последствии отказа, а также ранжирование рисков [3].
Основные проблемы внедрения RBI-анализа: нехватка квалифицированных кадров, которые будут выполнять сбор данных и анализ рисков, не выполнение персоналам выданных рекомендаций по снижению рисков и сложность расчетов (решается приобретением специализированного программного обеспечения).
Заключение
В статье были рассмотрены три методики ТОиР. Стоит отметить, что данные методики могут применяться в зависимости от типа оборудования. Например, RBI может использоваться для статического оборудования, RCM – для динамического оборудования[4]. Также методики можно внедрить не полностью, а частично. После принятия решения об имплементации той или иной методики требуется обязательно обучить персонал. Уровень квалификации персонала – ключевой фактор качественного использования методик.
Литература
- ГОСТ Р 55234.3–2013 Процедуры проверки и технического обслуживания оборудования на основе риска. М.: Стандартинформ, 2014.
- ГОСТ Р 27.606–2013. Надежность в технике. Управление надежностью. Техническое обслуживание, ориентированное на безотказность. М.: Стандартинформ, 2014.
- AB–505 Risk-Based Inspection Requirements for Pressure Equipment, 24 AUG 2017.
- SAE JA1012 A Guide to the Reliability-Centered Maintenance (RCM) Standard, Society of Automotive Engineers, 2002.
Выходные данные статьи
Абазьева М.П. Обзор методик техобслуживания и ремонта оборудования системы управления производственными активами предприятия // Корпоративные информационные системы. – 2021. – №3(15). – С. 13-19. – URL: https://corpinfosys.ru/archive/issue-15/117-2021-15-plantmaintenance
Об авторе
![]() |
Абазьева Мария Павловна – руководитель проектов внедрения корпоративных информационных систем. Эксперт по направлению технического обслуживания и ремонта оборудования. Имеет 10-летний опыт работы с программными решениями на базе SAP. Принимала участие в проектах имплементации ERP-систем в транспортных, нефтяных и металлургических компаниях. |
Статьи выпуска №15
- Изменения в правовом регулировании ИС в 2021 году;
- Обзор методик технического обслуживания и ремонта оборудования;
- Cutover-план в проектах внедрения ERP-систем (Часть 2);
- Agile Kanban для автоматизации работы городской больницы (часть 1);
- Автоматизация работы врача терапевта (часть 1).